Flux Core vs Mig Welding – Flux core welding and mig welding are advanced welding processes that are used for joining most metals. These processes are also known as arc welding and continuous welding. Flux core and mig welding are similar when it comes to the way they work. However, they have different pros and cons that should be considered before making a decision. In this article, we explain the differences between flux core welding and mig welding and help you in making an informed decision about which one to choose for your next welding project.
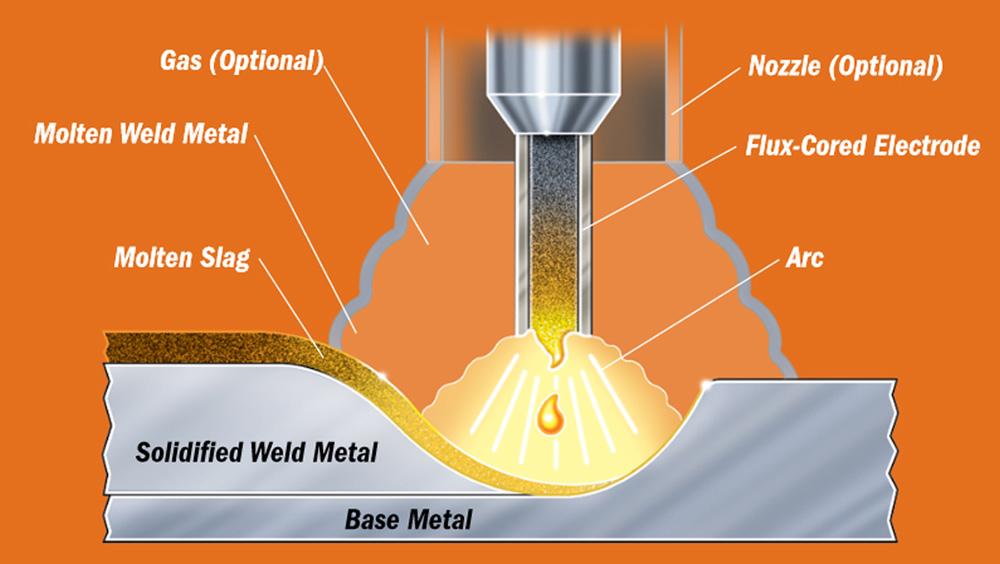
Flux cored electrodes (Flux Co-Electrodes) and metal-infiltrating arc welding (MIG welding and TIG welding) are both welding processes that make joints between two pieces of metal. The difference is in the way the two processes make a weld. MIG welding has a clean surface and produces a smooth weld. TIG welding has a fine wire diameter and produces a weld with a fillet.
Flux core electrodes are nickel-based electrodes that are almost exclusively used in the MIG and TIG welding processes. Since it is a modern welding process, MIG and TIG welding are both more common than arc welding. An average home handyman can learn how to weld using both processes. The only difference is the type of welding equipment that you need to use. Let’s take a look at the best types of welding equipment for MIG and TIG welding to help you decide which one is right for you.
Flux Core vs Mig Welding: Which One is Better?
Flux core welding and mig welding are two different methods of welding. However, they have a lot of similarities, and in many cases, they can be used interchangeably. When looking for the best tool for the job, the choice can sometimes be difficult. Today, we will be comparing flux core and mig welding in order to determine which is the best for the job. If you are reading this, there is a very high chance that you are aware that mig welding and flux core welding are two of the most common welding methods.
In fact, you may already have an opinion on which one of these welding techniques is better. Or, you may not even know the difference and would like to know more before you make a choice. So, before we dive into the details of how the two compare, let’s take a quick look at their common uses, pros and cons, and which one is the best for you.
What is flux core welding and mig welding?
Flux core welding is a process of joining metals using a non-consumable, solid-state wire. This process generally uses a flux-cored wire. The wire is driven into the base metal and swells up like a sponge, taking in the metal’s atoms and transferring them to the surrounding metal. This process is repeated many times until the two pieces of metal are welded. Generally, flux-cored welding is used for joining dissimilar materials where the weld will not require a high strength weld and a smooth surface is not required. Mig welding is a method of welding using a high-frequency current. Mig welders use high-frequency metal electrodes to create a weld bead. This process is generally used on metal, including steel, aluminum, cast iron, and stainless steel.
Differences between flux core welding and mig welding
The main difference between flux core welding and mig welding is the type of current used. Flux core welding uses a solid-state wire that is filled with a powdered metal that absorbs the current and melts to form the weld bead. Mig welding uses a high frequency current to create a weld bead by melting the electrode and depositing the melted metal onto the workpiece. Flux core welding is generally more accurate while mig welding is generally faster. Choose the method that works best for the application.
Flux core welding – the pros
– Long Weld Duration: The flux core wire can be used for up to 30 seconds before it becomes too short and becomes a short-circuit. The weld bead created with this wire can then have a very long life, often lasting over 200 amps. – Non-Consumable Wire: The wire used in flux core welding is a solid-state wire. This means that there are no consumable parts and so it will not be lost due to lack of spooling. – High Throughput: Flux core welding equipment can be used for high-throughput welding. This means that it can create multiple welds at a time.
Mig welding – the cons
– Heat Sensitivity: Mig welders are generally more sensitive to heat. Thus, it is advisable to use them only where proper ventilation is provided. – Lack of Control: Mig welding is generally not as accurate as the solid-state welding process. You will not get the same level of control with mig welding as you would with flux core welding. – Cost: Mig welders are generally more costly than flux core welders. – High Heat Sensitivity: Mig welders are generally more sensitive to heat. Thus, it is advisable to use them only where proper ventilation is provided.
Which one is better for your project?
A project is different for every person and every person has a different reason why they want to weld. There are a few things you can look out for when deciding which method to use. – Strength of Weld: The strength of the weld is one of the most important things to consider when comparing flux core and mig welding. Since both processes use non-consumable wires, the strength of the weld depends on how thick the base material is. Flux core welding generally applies to joining materials that are not very thick, so the weld will not be as strong as a weld made with a consumable wire. – Usability: The usability of the process also plays a part in choosing the correct method. Both flux core and mig welding require a certain level of skill in order to create a quality weld. The more experience you have with your chosen method, the easier it will be to use it. – Cost: The cost of your project is also a huge factor to consider when choosing the best welding method for your application.
Final Words
After reading this article, you should now have a much better idea of the differences between flux core and mig welding. These two methods can be used to weld a variety of metals, making them great for a variety of projects. Flux core welding is generally more accurate while mig welding is generally faster. Choose the method that works best for the application. If you are unsure which one to use, it is always good to check with your local welding supply store to get some advice.
Like this:
Like Loading...
Related